Swiss-based Datwyler opens $100 million Delaware factory
A first-of-its-kind medical supply manufacturing site in Middletown will eventually employ 120 workers in an ultra-clean assembly line.
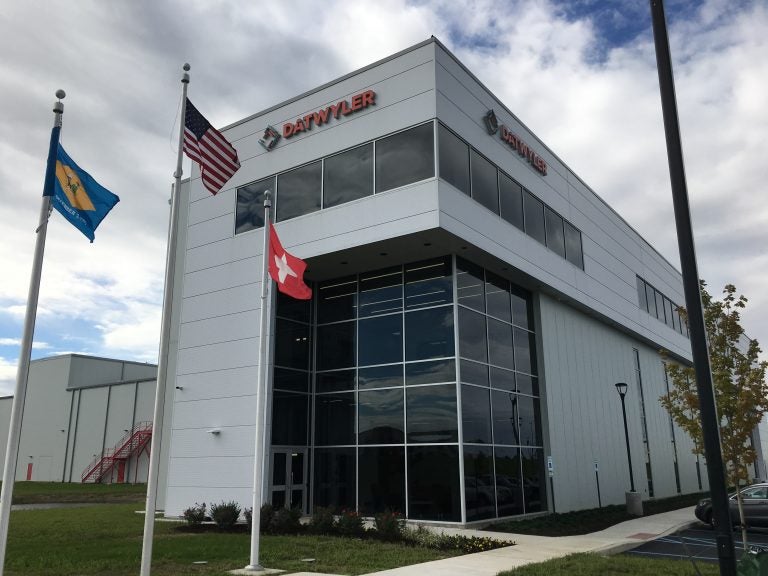
Swiss-based Datwyler's new facility in Middletown, Delaware is the company's first facility in the U.S. to feature its "first line manufacturing" process. (Mark Eichmann/WHYY)
Swiss-based manufacturer Datwyler has opened its $100 million medical supply factory in Middletown, Delaware, where it expects to employ 120 employees when the nearly 300,000-square-foot facility is fully functional by the end of the year.
The company took reporters on a tour of its new facility on Thursday morning to show off the ultra-clean assembly line many of those employees will be working in as they manufacture rubber and synthetic container caps and syringe components designed not to cause contamination.
When it comes to medical packaging of expensive pharmaceuticals, avoiding contamination is of preeminent importance. That’s especially true for medicines that are produced in small batches.
Datwyler’s “first line standard” for cleanliness was first established in 2009 at its facility in Alken, Belgium. It’s a process senior executive vice president Dan Stefanoiu says “has been accepted today by the industry, by the pharmaceutical companies as the best manufacturing environment for elastomer components in the world.”
Datwyler’s U.S. operations leader David Clark said the Middletown site was selected over other major cities, including Boston and San Francisco.
“The universities [were] part of the edge,” Clark said. “Also Middletown as a town was very good. The mayor helped us out a lot.”
The company received a $2.4 million grant from the Delaware Strategic Fund to help build the $100 million facility. The company is also eligible for more than $700,000 in performance grants as it hires more than 100 full-time workers.
The first line standard is a proprietary system Datwyler uses to keep the production line area as clean as possible, and the Middletown site is the first in the U.S. to use these protocols.
The nuts and bolts of the production machinery are kept behind walls so they can be maintained and adjusted without disturbing the clean room standards of the line. The traditional assembly line is divided into separate rooms that have graduated levels of cleanliness protocols and air quality. The final room in the process is rated ISO Class 5, which means it can have no more than 3,520 particles equal to or larger than 0.5 microns per cubic meter of air.
In another effort to keep the process clean, the line is completely paperless — even wooden pallets are replaced by plastic ones to reduce particulate contamination. It’s all part the company’s goal of keeping its products as clean as possible.
“To meet our quality requirements that the market needs for these high-end rubber components for injectable drugs, we have developed over the years a manufacturing concept which builds in the quality through the design,” Stefanoiu said. “Most important is that these products should in no way interfere with the drugs, the injectable drugs.”
Officials said the facility was built with expansion in mind.
“As our sales increase year over year, we’ll bring in new machinery,” Clark said.
WHYY is your source for fact-based, in-depth journalism and information. As a nonprofit organization, we rely on financial support from readers like you. Please give today.