Chemical Safety Board says PES refinery explosion ‘did not have to happen’
The Chemical Safety Board says if recommendations made after a California refinery explosion had been followed, the South Philly site might not have burned.
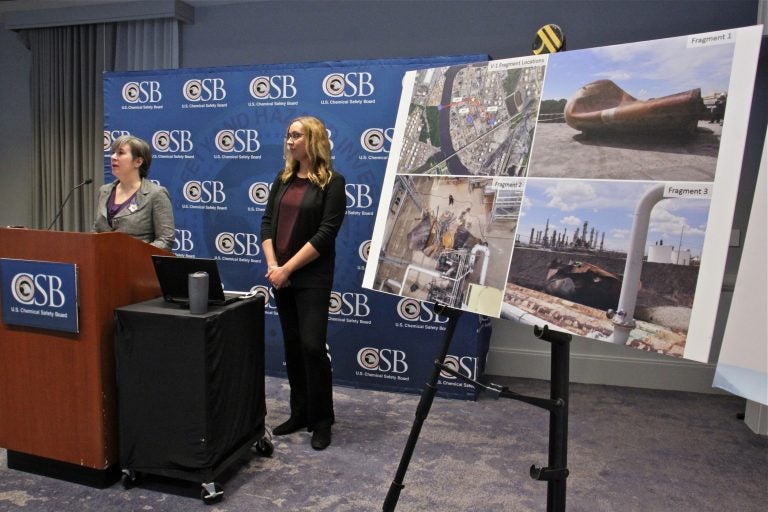
Kristen Kulinowski (left), interim executive of the U.S. Chemical Safety Board, and Supervisory Invetigator Lauren Grim, talk about the causes and results of the June 21 fire and explosion at Philadelphia Energy Solutions refinery. (Emma Lee/WHYY)
An outdated piece of pipe that had corroded so much its sides were the width of half a credit card led to the catastrophic explosion and fire at the Philadelphia Energy Solutions refinery in June, according to a new report out Wednesday by the Chemical Safety and Hazard Investigation Board.
The incident released a dangerous chemical, hydrofluoric acid, although no known injuries related to that release occurred.
“We are all very fortunate that there were no fatalities or serious injuries as a result of this catastrophic incident,” said the Chemical Safety Board’s interim executive, Kristen Kulinowski. “But I want to emphasize that we at the CSB are very aware that this event has shaken those that live and work within and around the refinery. Here in Philadelphia, the layoffs and announced closure of the facility means the elimination of about 1,000 jobs as well as an unknown economic impact on the surrounding community. This didn’t need to happen.”
Hydrofluoric acid, or HF, is one of the most dangerous industrial chemicals in use. Exposure can lead to serious injury or death. It can also corrode pipes. The Chemical Safety Board report says the faulty pipe that led to the explosion and fire was installed in 1973 and was grandfathered when new standards were put in place in 1995.
Swallowing just a small amount of HF or getting small splashes on the skin can be fatal, according to the Centers for Disease Control and Prevention. In a gaseous state, the CDC says, low levels of HF can irritate the eyes, nose and respiratory tract. Breathing it at high levels “can cause death from an irregular heartbeat or fluid buildup in the lungs.”
About 48 refineries across the country, including two currently operating in the Philadelphia region, use HF as a catalyst to make high-octane gasoline. Kulinowski said pipe corrosion also led to similar incidents at refineries in other parts of the country.
“We’re concerned that the next time there’s a massive explosion and debris is strewn, we’ve seen this three times, that we’re not going to be so lucky. And the major vessel that contains the HF will be compromised.”
After explosions in California and Utah, Kulinowski said, the Chemical Safety Board recommended that industry inspect all pipes, not just representative sections. But it does not have the power to demand those inspections. The American Petroleum Institute sets the safety standards for how to process and utilize HF.
“We need to focus on making sure that this kind of explosion at a refinery doesn’t happen anymore. Because it’s just a matter of time before the facts are a little bit different, and people die or are critically injured or there’s an offsite consequence, Kulinowski said.”
The CSB is not a regulator — its mandate is to conduct investigations of accidents and provide safety recommendations. Kulinowski said that the investigation at Philadelphia Energy Solutions is ongoing and that recommendations should come as part of its next report, due out in early 2020.
“The PES refinery is 150 years old,” she said. “The piping component that failed was installed in the 1970s, and although parts of the piping circuit had been inspected as recently as 2018, the specific component that failed has not been inspected for corrosion in the past 45 years.”
There are “striking similarities” to a 2012 explosion and fire at the Chevron refinery in Richmond, California, she said. In the CSB’s Chevron report, the agency recommended that California regulators require “damage mechanism hazard reviews,” which examine risks associated with corrosion. California has a state agency that oversees worker safety, while Pennsylvania relies on the federal Occupational Safety and Health Administration.
“The board remains concerned that the next time there is a major explosion at a refinery that uses HF for alkylation, workers and those living nearby will not be so lucky,” Kulinowski said.
PES chief executive officer Mark Smith said the company is “committed to working with the CSB to make certain that it understands the agency’s concerns.” But he said the CSB recommendations from the Chevron incident did not apply to the Philadelphia refinery.
“PES understood the CSB as noting that it had previously investigated other refinery incidents that resulted from corrosion,” Smith said in a statement. “These incidents and resulting CSB recommendations, however, were tied to specific types of corrosion or damage mechanisms. For this reason, previous CSB recommendations are not directly relevant to this incident. As noted by the CSB, inspection data for representative monitoring locations on the relevant piping segment did not indicate a problem.”
Hurling tanks
Workers and residents of the neighborhood surrounding the PES refinery also avoided potential catastrophes from flying debris. Three explosions occurred after leaked propane caught fire. The largest explosion sent a 38,000-pound vessel — about the same weight as a firetruck — nearly half a mile through the air across the Schuylkill River, where it landed on the waterway’s banks, near the company’s tank farm.
Two other large pieces, one 23,000 pounds and another 15,500 pounds, landed in the refinery. Kulinowski said it was lucky those pieces did not hit any parts of the operation that could have caused even further damage. A fourth piece has still not been recovered because it lies in an area that remains inaccessible.
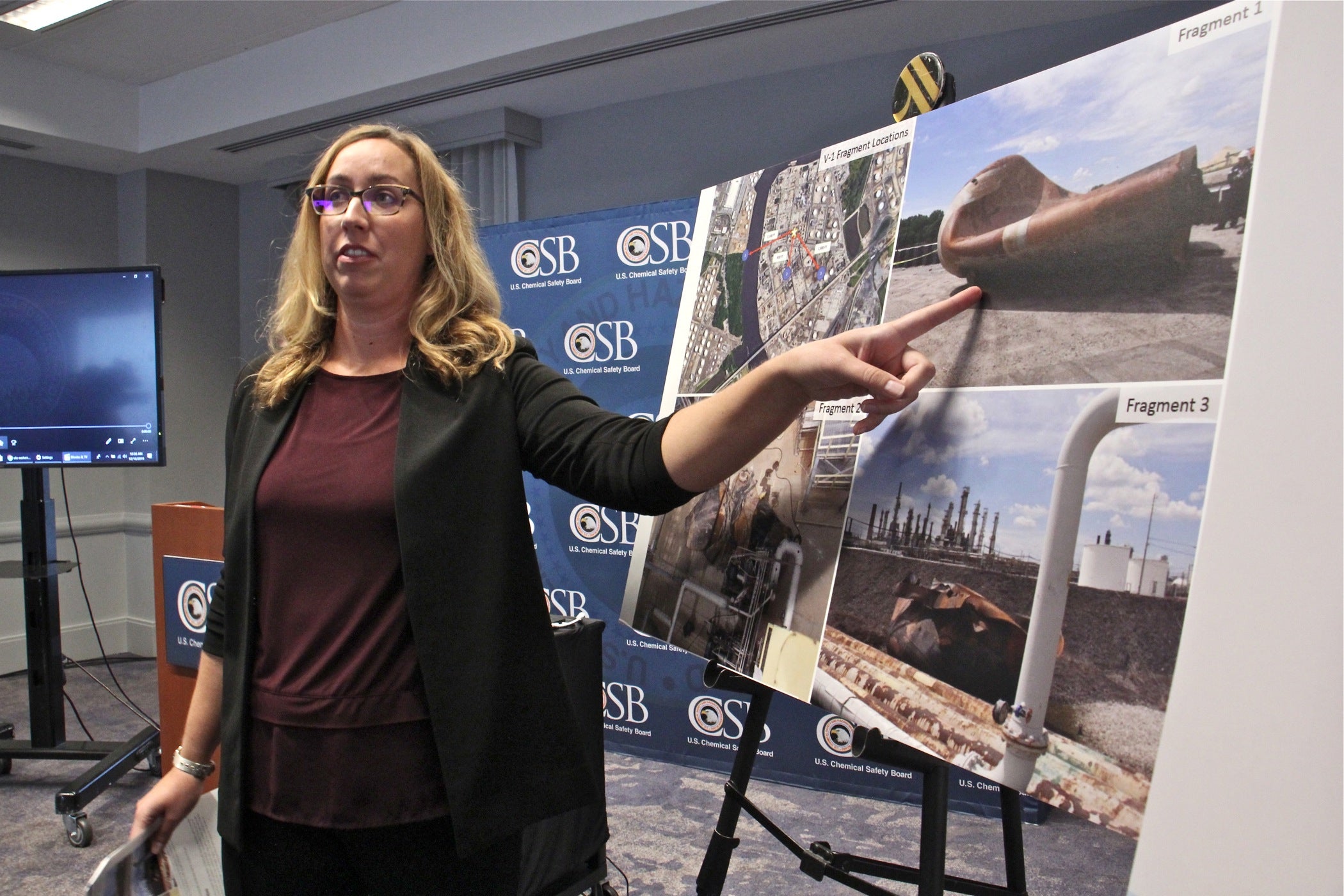
PES estimates that the incident released 676,000 pounds of hydrocarbons, most of it — about 608,000 pounds — burned in the fire and explosions.
The CSB report says an estimated 3,271 pounds of hydrofluoric acid was released into the atmosphere, while the refinery’s water spray system contained about 1,968 pounds of HF, which was detected by the refinery’s own air monitors. City officials had previously reported they did not detect any HF escaping. Kulinowski would not comment on issues surrounding the reliability of the city’s air monitors.
She said the refinery’s own system — known as ‘Rapid Acid Deinventory” — that evacuated the bulk of the toxic HF did work and prevented further injuries.
“I’m impressed that industry had its act together, that it has a RAD system, and that they activated it in a timely fashion,” said Ron Koopman, a physicist and expert in chemical safety. “That’s new turf for industry taking responsibility. Because as far as I know … this is the best response that I’m aware of.”
As a senior scientist at the Lawrence Livermore National Laboratory, where he worked for 36 years, Koopman conducted the definitive experiment on the release of hydrogen fluoride back in 1986. He said the HF that was released at PES was likely dispersed by the intense explosion.
“The explosion is nasty — it could kill people, but it’s not the principal hazard,” he said. “It’s the toxic gas [HF] that could continue to be toxic downwind. Sometimes, the explosion and the fire is your friend.”
Koopman’s experiment in 1986 released 1,000 gallons of HF at a Nevada test site. The results shocked him. A video of the experiment shows white billowing clouds of poisonous gas expanding and traveling rapidly across the desert. Highly toxic levels of HF were detected miles away.
Refineries typically have water spray mechanisms to contain HF, which were also activated at PES. Koopman said fast action is critical because once the HF is airborne, it can kill people at high concentrations.
“The [workers] are my heroes in this process,” he said.
What started the explosion
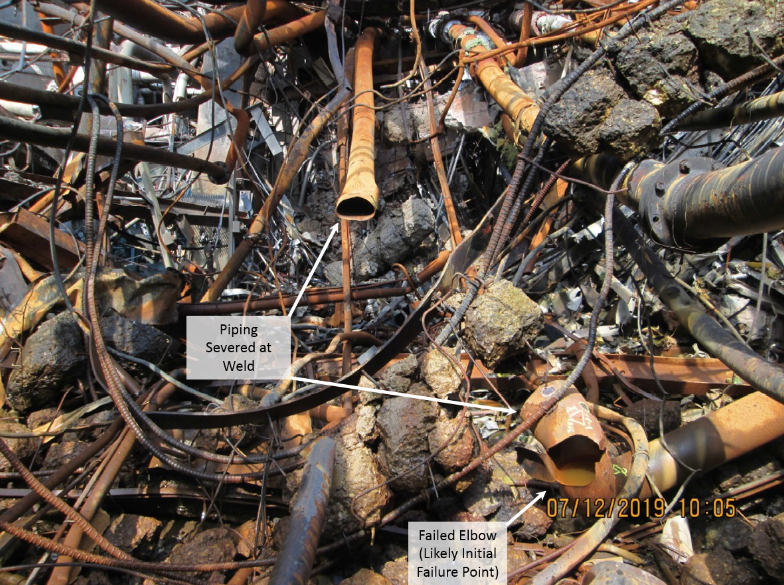
The June incident at PES began when a 90-degree piece of pipe known as an “elbow” ruptured, releasing fluid containing hydrocarbons and HF. The pipes in the refinery’s alkylation unit are monitored at specific spots — known as “condition monitoring locations,” or CMLs — to measure for thickness. The ruptured elbow, however, was not a CML, and thus its thickness had not been monitored.
PES had a policy that any pipe thinner than 0.18 inch would be replaced. The Chemical Safety Board’s investigation found that the ruptured pipe was only 0.012 inch thick — less than a tenth of the thickness that would have triggered a replacement.
John Jechura, professor of practice at the Colorado School of Mines, said deciding where to test for corrosion is always a probability issue.
“You can’t check every square inch of pipe,” he said.
As a rule of thumb, he said, the areas most vulnerable to corrosion — and thus potential cracks and leaks — are places in the pipe where there is a change in the flow direction: T’s, Y’s, and elbows. Given that he was not involved with the PES plant, Jechura said he couldn’t say why the ruptured elbow was not an area that was monitored more closely.
CSB supervisory investigator Lauren Grim, who led the PES inspection, disputed Jechura’s statement that not every piece of pipe could be inspected.
“Actually, California has updated its safety regulations to require these damage mechanism reviews,” she said. “And some CSB leadership is actually talking to California regulators about that this week”
Grim said the requirement to conduct 100% inspections could be focused.
“This kind of variable corrosion rate isn’t an issue in all parts of the refinery,” she said.
Another issue was the pipe material. The pipes in the alkylation unit were installed in 1973, when industry standards did not specify how much nickel or copper they should contain. In 1995, however, those standards were updated, specifying that pipes should be no more than 0.4% each nickel and copper. The ruptured pipe contained 1.74% nickel and 0.84% copper.
Petrochemical-industry standards are largely self-directed, and so any pipes installed before the regulations were updated in 1995 were grandfathered in, despite the fact that the American Petroleum Institute’s own recommended practice for “Safe Operation of Hydrofluoric Acid Alkylation Unit,” last updated in May 2013, states: “HF corrosion has been found to be strongly affected by steel composition and localized corrosion rates can be subtly affected by local chemistry differences.”
Mike Wilson, national director for occupational and environmental health at the BlueGreen Alliance, said that lack of oversight has meant refineries are not sufficiently required to invest in maintaining and improving safety.
“This is certainly the case with the federal standard for refinery safety, which is 27 years old and far outdated,” Wilson said. “It requires very little by refiners to actually fix process-safety hazards, such as corroded piping systems.”
Hydrofluoric acid is regulated by both the Environmental Protection Agency and the Occupational Safety and Health Administration.
OSHA does so under the Process Safety Management of Highly Hazardous Chemicals. The EPA’s Risk Management Plan Rule governs public disclosures surrounding the use and accidental release of toxic chemicals, as well as emergency response. The CSB sent a letter to the EPA earlier this year urging it to require safer alternatives. Kulinowski said the agency has not replied.
The Obama administration toughened risk management rules, but Trump’s EPA says it wants to roll back some of the new provisions, including the requirement that industry assesses the use of safer alternatives.
However, other standards — like pipe maintenance and composition — are set by industry groups, and refineries generally police themselves.
According to the EPA, between 2007 and 2017, there were 1,517 reportable accidents at facilities using hazardous chemicals — nearly 150 incidents a year over 10 years. Nearly 500 of those accidents affected residents in surrounding communities.
“We don’t hear about them, but they’re significant enough to threaten people’s safety, if not their long-term health,” Wilson said.
He noted that in the explosion at Chevron’s Richmond, California, refinery, engineers had recommended on six different occasions that the company replace pipes that were out of date, but Chevron management decided not to replace them.
“The CSB continually points out that the most obvious causes of a major incident, such as a corroded pipe, are not what actually caused the incident,” Wilson said. “Major industrial failures like this are nearly always the consequence of management decision-making and the way safety is prioritized or not.”
Wilson noted that until the CSB report is complete, he couldn’t say whether Philadelphia Energy Solutions faced a similar issue with regard to safety culture.
Koopman, the physicist and chemical-safety expert, agreed that self-regulation may not be the best way to ensure that industry employs the best practices to keep workers and nearby residents safe.
“Luck has saved a lot of people in this business,” he said. “You would hope that we could do better than luck. But when it comes down to it, luck is a good thing.”
—
WHYY’s Dana Bate contributed reporting.
WHYY is your source for fact-based, in-depth journalism and information. As a nonprofit organization, we rely on financial support from readers like you. Please give today.