These pre-employment programs could be a model for Rebuild’s jobs goals
The Advanced Manufacturing Boot Camp, along with PennAssist, a program that launched in summer 2017, are viewed as experimental models for what Rebuild aims to accomplish.
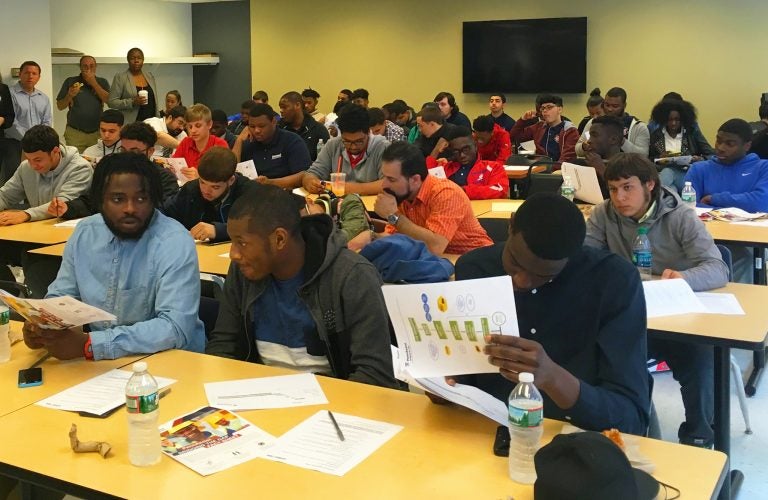
A May 2017 kickoff event for PennAssist's pre-employment program, which had a younger group of 44 participants. (Courtesy of Philadelphia Works)
This article originally appeared on PlanPhilly.
—
At 36 years old, Herbert Robinson wasn’t just looking for a job. He wanted a career.
Earlier this year, his resume looked pretty patchy. He had some manufacturing experience — making flak jackets and lockers for the Army, working on an assembly line of UNICOR, a prison labor company, inside a federal detention facility — but not much else.
Since moving back to Philadelphia in March after his release, Robinson explored all the free career fairs and job-training programs that he could, attempting to make up for lost time. “I’m still in that beginning stage of finding out where I want to be and what I want to do,” he said.
Now, the job search is over. The career search, too.
Last month, Robinson became one of a dozen graduates from a new manufacturing boot camp run by PA CareerLink in collaboration with the Southeast Regional Advanced Manufacturing Partnership, a network of about 60 companies trying to address looming gaps in the regional manufacturing-labor supply. Despite the decades-long decline of manufacturing jobs in the Philadelphia region, the prospect of filling more than 100,000 available positions is making employers anxious. According to a 2012 report cited by Governor Tom Wolf in his 2015 plan to restore manufacturing jobs statewide, more than four out of five Pennsylvania manufacturers see notable skills gaps in their workforce.
But that’s only one reason why the program Robinson recently completed has drawn the gaze of lawmakers. The boot camp is being viewed as a possible forerunner to pre-employment programs that will be part of Mayor Jim Kenney’s Rebuild initiative, previously billed as a $500 million effort to upgrade parks, recreation centers, libraries and playgrounds but now projected to be somewhat smaller in scope.
The Kenney administration has negotiated two memorandums of understanding with the local building trades that outline pathways for prospective laborers to acquire work experience on Rebuild sites and be given the opportunity to join labor unions — should they want to — in the long run. One program is being designed for individuals with preexisting manufacturing experience, such as Robinson, who will work on Rebuild sites via job placement with the Philadelphia Redevelopment Authority. That’s being dubbed the PRA Talent Development Pipeline. A second, yet-to-launch program, called PHL Pipeline, will cater to young adults with no experience in the construction industry, providing them with job training on par with what union apprentices receive.
The Advanced Manufacturing Boot Camp, along with PennAssist, a program that launched in summer 2017, are viewed as experimental models for what Rebuild aims to accomplish. Both were organized by Philadelphia Works, a quasi-public nonprofit that collaborates closely with City Hall on workforce development initiatives. Philadelphia Works will be involved in the design of both PHL Pipeline and the program that will be run through the Redevelopment Authority.
“In my mind, we were thinking that if we were successful with PennAssist — with the boot camp, the wraparound services, the counseling, and the workforce development components — then we could have a model for Rebuild that would include getting participants a seat in the apprenticeship classes of these unions,” said Pat Clancy, president of Philadelphia Works.
Addressing two different cohorts — a smaller (16 participants), older group in the Advanced Manufacturing Boot Camp, and a larger (44 participants), younger group in PennAssist — the experiences of both programs has yielded wisdom ahead of Rebuild.
In the case of PennAssist, the cohort was made up of former public school students who had completed Career Technical Education (CTE) courses in a variety of skill areas, such as heating/ventilation/air conditioning, plumbing, and welding. PennAssist began with a three-week boot camp in the classroom that targeted skills development for the apprenticeship tests that are prerequisites to union membership. The program helped all the participants get driver’s licenses. But it was also designed to imbue the young men with soft skills that are important in the workplace.
“We’re talking about 18-year-olds. These kids are not used to going to work at a major union company,” said Eric Ward, a career navigator for CareerLink and the point person on PennAssist. “We have to understand how to reach these young people life-wise, not just job-wise. Otherwise, none of this will matter if we wind up losing them in two weeks or two months after their placement.”
Ward drew upon expertise in areas such as trauma-informed therapy, conflict resolution, and black male engagement to build relationships with participants that went beyond tutoring. All of them had his cell phone number. Before being placed with various unions, most of the PennAssist participants completed a stint of transitional employment in the private sector, providing them a trial run of sorts in advance of working in front of union supervision. Of the 44 participants, a year later 40 are working as apprentices with local labor unions or have been placed in transitional employment in the interim while they wait to take — or retake — the tests.
There were bumps along the way. Originally, the timeline for placing graduates on work sites, whether in apprenticeships or employment, was expected to be much shorter. The learning curve for some CTE grads was steeper than expected. And finding quality matches for each member of the cohort — either with unions or employers — proved challenging.
“What we saw with PennAssist was that when you have 44 youth in the program, it will stretch resources thin in terms of finding employment for those youth,” said Christopher Gibbs, community engagement and outreach specialist for CareerLink, who worked on both programs. “Lowering the amount of participants with the Manufacturing Boot Camp allowed us to provide more individualized, one-on-one services for them.”
The Advanced Manufacturing Boot Camp intentionally accepted fewer candidates. Only 16 of 97 prospective participants were accepted, compared to nearly a 60 percent acceptance rate with PennAssist. Another difference was hosting the training sessions down at the Philadelphia Shipyard, rather than in a classroom setting in Center City. All the boot camp participants had to make it to South Philadelphia by 7:30 each morning for their courses, which covered everything from writing cover letters to crafting post-interview thank-you notes, to technical skills. Using the Navy Yard as the primary location for the program also allowed participants to see active manufacturing workplaces, such as Rhoads Industries, an industrial fabrication, installation and maintenance firm.
“Going to the shipyard, we were shown how they manufacture ships. Employers were able to ask us questions. They were able to show us their facilities,” Robinson said. “They showed us all the positions that would be available: quality-assurance work; maintenance work; operating a machine. They gave us different scenarios, and we went through the pathways or ladders of moving up.”
Just one month after the Manufacturing Boot Camp finished, more than half the participants are now fully employed, including Robinson. On Monday, he began a full-time position as a plasma assistant working for Sandmeyer Steel Co. in the Northeast.
“The boot camp was a big help to me,” Robinson said. “It did wonders for me.”
The real results of the programs won’t be known for years to come, given their shared goal of producing sustained careers, not simply jobs. But Philadelphia Works has been impressed with the early returns. It plans to launch a boot camp in conjunction with SEPTA that will be based on a similar format.
Though a reduced-size program might yield better results, it also begs the question whether successful pre-employment programs must be inherently small — or if they can ever scale up to the point that they’re able to make a dent in the racial disparities of the manufacturing and construction workforce in Philadelphia. The most recent publicly available diversity data for the building trades show that a majority of the unions had less than 10 percent African American membership.
It’s possible those answers won’t be known until Rebuild plays out.
This article has been updated to clarify Philadelphia Works’ role in two future programs.
WHYY is your source for fact-based, in-depth journalism and information. As a nonprofit organization, we rely on financial support from readers like you. Please give today.