Retooling Habitat for Humanity in Delaware [video]
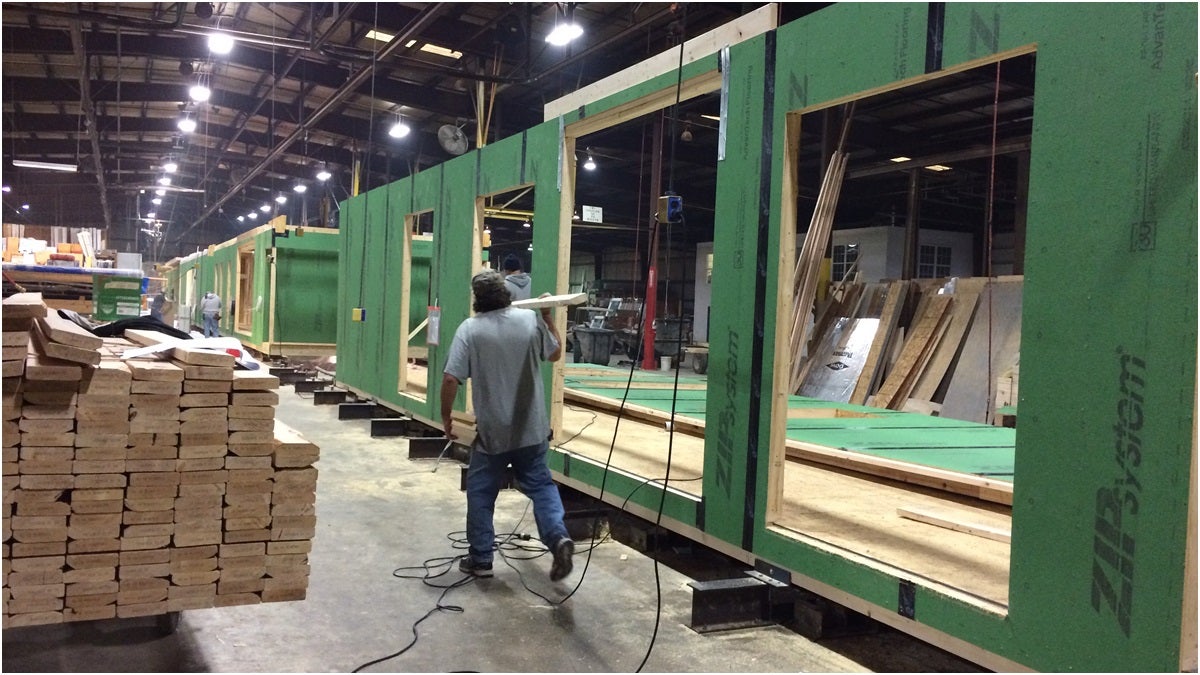
Homes being manufactured inside Beracah Homes' Greenwood, Del. plant (Shirley Min/WHYY)
Demand for quality housing remains at a premium, which is why Habitat for Humanity of New Castle County is tweaking its formula for building homes.
For decades, the nonprofit’s construction arsenal consisted of three pillars: new construction, rehabs and recycles. New construction is pretty self-explanatory, rehabs are homes that Habitat guts and renovates, and recycles are Habitat homes that come back into the nonprofit’s possession either through default or because the homeowner wants to sell.
But the New Castle County chapter is adding a fourth pillar – pre-fabricated modular homes.
“When we sit down to plan our construction process for the year, we consider the areas where we have obligations to build, and we certainly are looking at dollars,” said Michael Synczyszyn, Habitat’s director of construction. “Adding the modular piece to our overall construction skill-set allows us to maximize every dollar that comes into our organization and to stretch it.”
Habitat has built 22 homes in Middletown, which is about an hour from its Wilmington headquarters depending on traffic. CEO Kevin Smith said the majority of his volunteers are in northern New Castle County, and given Middletown’s location, it was not only tough to find volunteers on a regular basis to build homes from scratch, but it was also not cost effective from a staffing standpoint.
“One of the misnomers about Habitat, so you’re building houses with volunteers and so you’re saving money that way, and that’s partially true,” Smith said. “What people don’t understand is when you’ve got a volunteer coordinator, you’ve got a site supervisor and some assistants on staff, that overhead to manage all of those volunteers almost equals that savings that they’re providing.”
According to Smith, it can cost upwards of $165,000 to build a single Habitat townhome on site. Smith said implementing modular as an option will save anywhere from $5,000 to $15,000 per home.
“We are trying to save every penny we can because the bottom end for us is that we need to build an affordable house for the families that we serve. So every dollar that we save makes the house more affordable to the families that we’re looking to put into these homes,” Smith said.
Three modular homes to start
Sussex County-based Beracah Homes won the contract through a competitive bid process. The modular home builder is creating three homes for Habitat to start. A 1,456 square foot ranch that will be delivered to Newark and two duplexes that will be set up in Middletown.
“I know a lot of their methodology is to use a lot of on-site labor by volunteers and things like that. But I was excited about it because the process of building a modular home can assist them in doing it faster, and better and cheaper,” said Roger Collison, CEO of Beracah Homes.
Beracah manufactures their homes inside its Greenwood plant. Shielded from the elements, homes are framed, insulated, shingled and weather-proofed in a matter of weeks.
“We term our construction process ‘off-site, stick-built,’ built to the same local building codes as any residential or commercial builder would build to, we just do it in a different way,” Collison said. “We deliver it to the job site and we set it in between three and eight hours.”
Sweat equity
Traditionally, once you qualify for a Habitat home, you are required to put in 250 hours of sweat equity to help build your home. But if Beracah is doing all of the heavy lifting, how will Habitat’s homeowners work off their hours?
Synczyszyn said that was one of the challenges Habitat had to overcome in adding modular to its construction arsenal. However, once the home is delivered, he said homeowners can work off some of their hours putting the finishing touches on their modular homes, and work off the rest on other Habitat projects.”Habitat will never lose its need for volunteers or the piece of involving our homeowners in the construction process,” he said.
Because these are the first modular builds for Habitat, Synczyszyn said the nonprofit will be looking at how the cost savings match up against its preliminary projections. But ideally, Habitat would like to build four to five modular homes a year.
WHYY is your source for fact-based, in-depth journalism and information. As a nonprofit organization, we rely on financial support from readers like you. Please give today.