Streets Department wraps up Society Hill ADA ramps, ends headache
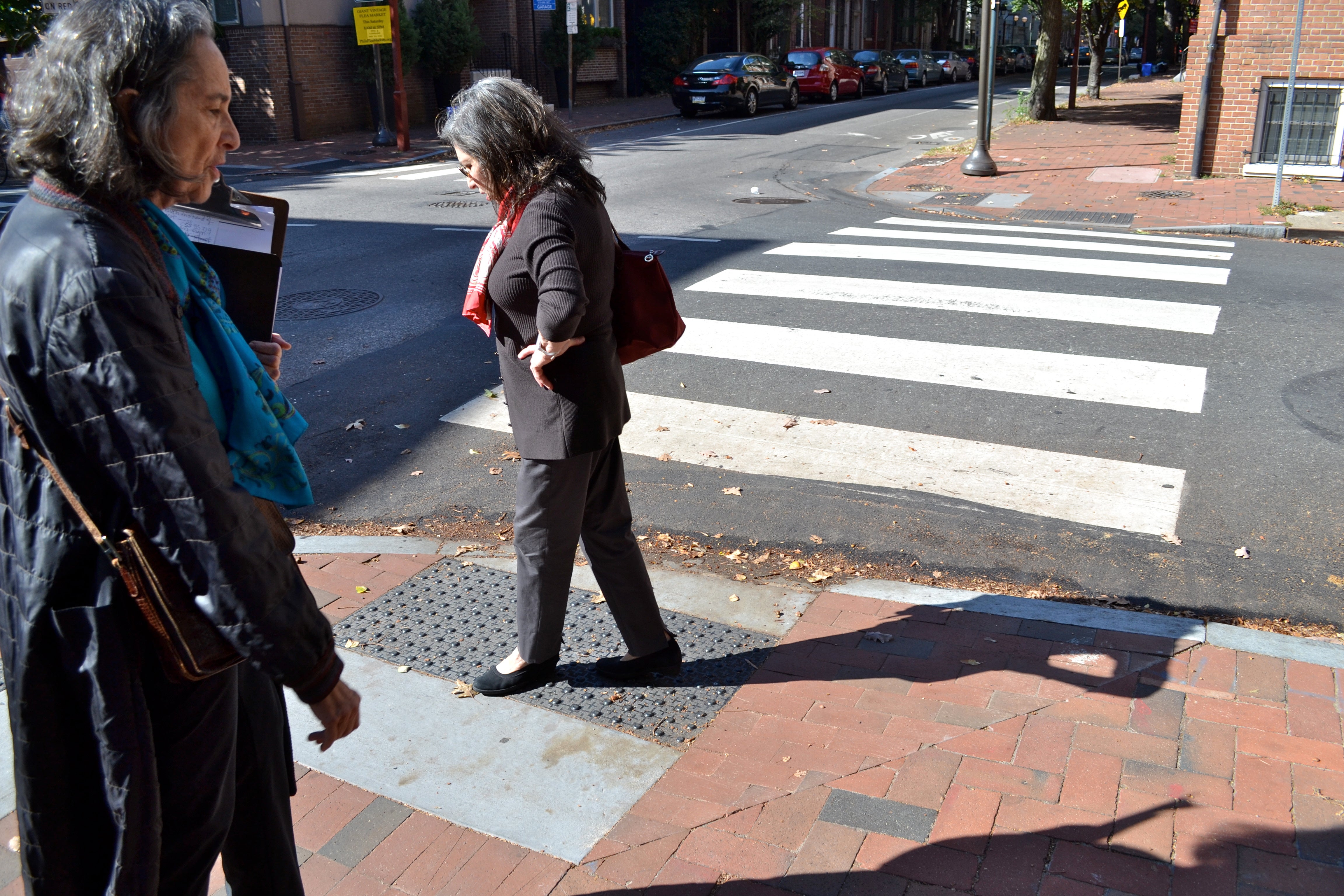
After years of work, negotiations and delays, the city has finished installing handicapped accessible curb ramps in Society Hill. The 488 ramps were installed, per federal requirement, on 327 corners and cost $3.3 million. While the work in this Old City neighborhood may be done, the road ahead is long. As the city repaves its street network, it must install handicapped accessible curb ramps at the majority of its 29,000 intersections.
In 2009, under the Americans with Disabilities Act (ADA), the federal government mandated that any time a street is resurfaced, the project must install handicapped accessible ramps built with an 8.33 percent grade and other stringent requirements. The first place the city encountered this mandate was Society Hill – “an awful place to start,” said Darin Gatti, chief engineer at the Philadelphia Streets Department.
The Streets Department had already planned to resurface the streets in Society Hill when the mandate went into effect and required that, because the streets were being paved, ADA ramps be installed. Gatti said adding ADA ramps to the public right of way was the right thing to do, but no one really knew what the work would entail until it started.
In Society Hill, as in other parts of the city, building ramps at a maximum slope of one-quarter-inch per foot can require lowering the surrounding sidewalk by as much as eight inches. For some historic homes, lowering the sidewalk means exposing fragile foundations. To protect these foundations from being exposed to the elements, the Streets Department decided to install cheek walls, which are essentially brick or concrete skirts between the building and sidewalk that prevent moisture from damaging the would-be exposed foundation.
But when the Streets Department installed a concrete cheek wall on a historic brick home and sidewalk at the corner of 4th and Delancey streets, the Society Hill Civic Association (SHCA) spoke up. The work came grinding to a halt.
“When we hit the brick is when we hit the problem,” Gatti said.
SHCA was concerned that concrete cheek walls would detract from the historic nature of the neighborhood and that they could not be removed without damaging the foundation. These concerns led to a “significant delay in the project because once you have a historic issue, the state says you have to stop and resolve it,” Gatti said.
The Streets Department went back to the drawing board and collaborated with SHCA. Together they decided the cheek walls would be avoided whenever possible. When necessary, cheek walls would be made with the same material as the sidewalk – either brick or concrete. Gatti said that, with the majority of homes in the neighborhood being 200 years old, give or take, it would have been nearly impossible to match the cheek wall bricks to the homes’ bricks.
“The preference was to avoid cheek walls if possible,” he said.
In total, the Streets Department installed approximately 103 cheek walls and 488 ramps. The ramps alone cost $3.3 million. To put that in perspective, the total paving project that prompted the ADA ramp work cost $5.7 million.
That is what has made the Streets Department and other city agencies apprehensive. Now, whenever the city repaves a street, it must install ADA compliant ramps at each of the intersections – a costly and time intensive addition to the street paving process. Last year, 67 percent of the city’s total paving budget went toward installing ADA ramps, and Gatti said the Society Hill ramps represents just one percent of the ADA work the city must complete.
“There’s a light at the end of the tunnel,” said Michael Carroll, director of engineering and special projects at the Mayor’s Office of Transportation and Utilities. “We just don’t know if it’s an opening or a train.”
Other SHCA concerns
The cheek walls were not SHCA’s only concern. SHCA wanted as little concrete used on the neighborhood’s brick sidewalks as possible, so the Streets Department agreed to build the “wings” of each ramp with brick. Because the ramps have to be at a very specific grade, the bricks had to be set like tiles in a bed of concrete, rather than vibrated into place in a mix of sand and concrete particles like typical sidewalks.
“We fought – we really did – to have more brick and less concrete on the ramps,” said Martha Levine, a SHCA board member who some SHCA members refer to as ‘miss streets.’
“We won,” Levine said. “It delayed everything, and everyone hated us.”
Other changes, like the color of the concrete, were made along the way. Now SHCA is concerned because the contractor splattered concrete on the neighborhood’s historic Franklin light poles – poles that SHCA spent $72,000 repainting in 2009. Gatti assured SHCA that the concrete will be removed.
Today the ramps have mixed reviews. “For people who are fine, they pose a big danger in snow and ice,” said Lorna Katz Lawson, chair of the SHCA zoning and historic preservation committee.
On a recent tour of the Society Hill ramps, Lawson toed a “too small” triangular brick.
“This doesn’t really meet the standard of workmanship,” she said.
Lessons learned
Whie Gatti said installing ADA ramps in the public right of way is the right thing to do, the stringent requirements do not always make sense. In some cases, ramps are required on sidewalks that are not ADA accessible because they are too narrow or too steep. Right now those issues are being addressed with exceptions to the rule. For instance, ramps are not required on the corners of cobble stone streets because those streets are not considered ADA accessible.
The time and effort spent in Society Hill should help the Streets Department save time as it installs ramps throughout the rest of the city.
“What came out of it was a policy that can be applied to the entire city,” Gatti said. “Basically we now have a standard.”
Even with a standard and the fact that neighborhoods with concrete sidewalks and fewer historic homes should be more conducive to the ramps, the Streets Department has its work cut out. The majority of the city’s 29,000 intersections must be updated. With four corners per intersection and costs averaging $15,000 per corner, the work ahead will be both expensive and time consuming.
“It’s going to take years,” Gatti said. “Every neighborhood is different, and they each have obstacles.”
But, he said, “We keep moving. We keep addressing problems as they come up. Every corner is an adventure for us.”
WHYY is your source for fact-based, in-depth journalism and information. As a nonprofit organization, we rely on financial support from readers like you. Please give today.