A Pa. company switched from sewing football jerseys to face masks. Workers walked off, saying the plan was unsafe
“It wasn’t about getting masks out to the public. It was about saving his company and making as much money as possible."
This story originally appeared on PA Post.
At first, Scott Hoffman thought the employee was half-joking.
It was mid-March, before the coronavirus had shut down the entire state of Pennsylvania, but Hoffman and the other workers at All Sports America could sense what was coming.
They wondered: What would happen to the 20 or so workers if the small sewing plant in Northumberland County had to shut its doors?
The worker’s idea was simple: All Sports America should start producing face masks instead of football jerseys and T-shirts. That way, the plant could stay open, an essential business helping respond to the pandemic.
Hoffman forwarded the employee’s idea up the chain, sending it to one of the company’s owners.
But it was the next day – March 19 — that the mask idea became critical to the company’s plan to stay open: Gov. Tom Wolf ordered all “non-life sustaining” businesses across the state to close their doors. Businesses could apply for a waiver to remain open, but otherwise would have to lock their doors until the coronavirus threat had passed.
Two days later, the company applied for one of the special waivers from the state Department of Community and Economic Development. The state denied the request at first, but approved it on April 2 after the company said in an email that it planned to produce face masks, according to department spokesperson Casey Smith.
For weeks, Hoffman worked with the company’s owners and his team to create different designs, adjust the sewing stations and prep for the production change.
It was during this transition that Hoffman found himself in conflict with All Sports’s majority owner and president, Richard Rock, over how to protect workers from potentially spreading the coronavirus at the plant.
Hoffman thought Rock was making changes for the wrong reasons.
“It wasn’t about getting masks out to the public. It was about saving his company and making as much money as possible,” Hoffman said. “And he didn’t care, you know, who got sick in the meantime.”
Hoffman thought the company misrepresented working conditions in its March 21 waiver application to the state. That application said fewer than 10 workers would be on duty at any given time. But Rock wanted more than 10 people sewing. The March 21 waiver application also described 50,000 square feet of space, enough for workers to spread out and practice social distancing. Hoffman said that number refers to the footprint of the entire building and its warehouse, while sewing would be done in a 2,100-square-foot room, he said.
Hoffman said he didn’t receive a copy of the March 21 waiver application until April 6, included as part of a packet of information that employees could provide to law enforcement in case they were questioned about why they left their homes during the governor’s shutdown orders.
He said he started looking at that application closely after Rock pressured him to add more workers and change the safety plan Hoffman had created.
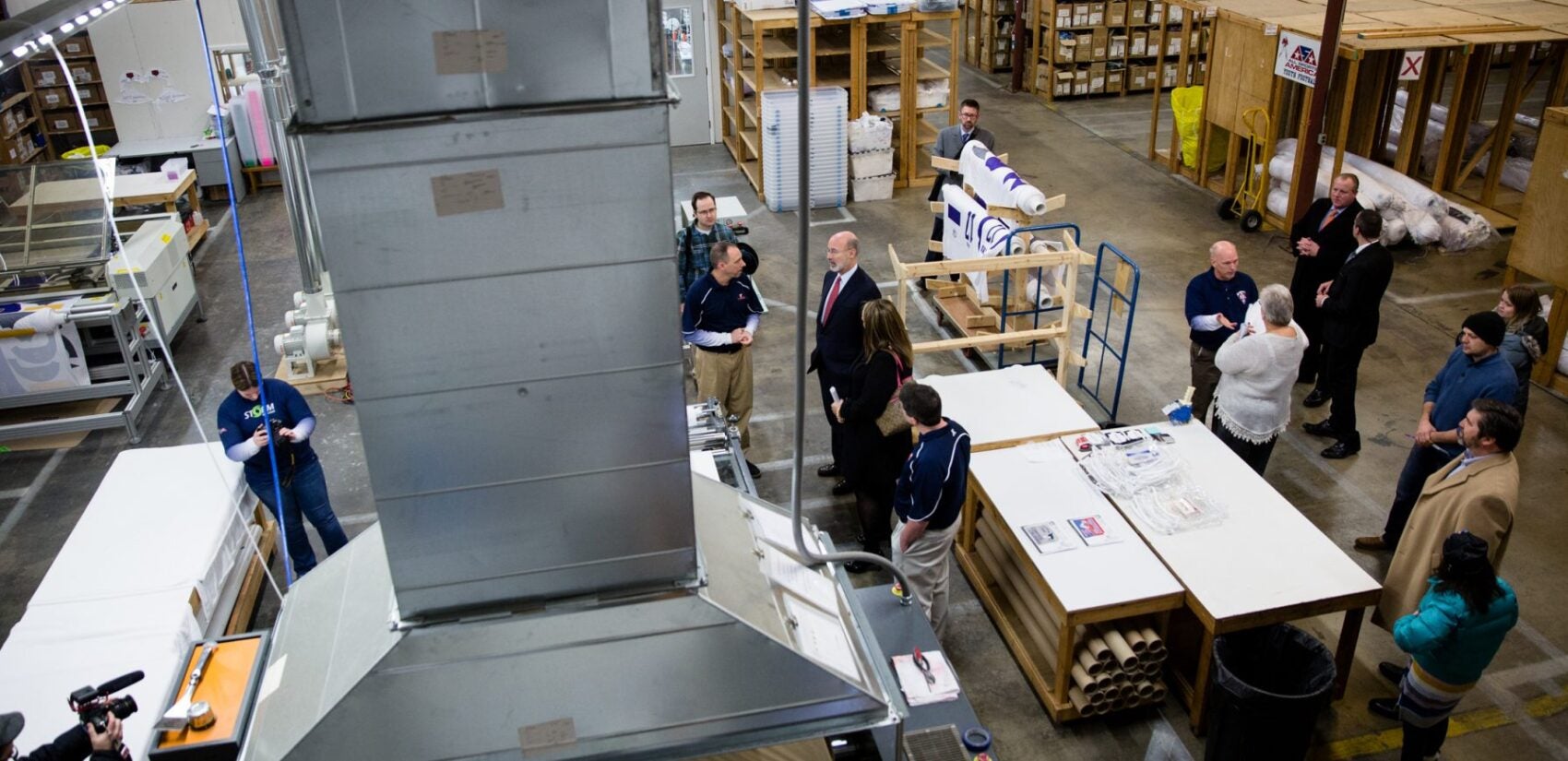
Hoffman’s safety plan proposed that six workers would work in the sewing room, each producing masks independently. But Rock proposed 14 people sewing at once, working in an assembly line with each person making just part of a mask.
Hoffman said 14 people working in the room at once wouldn’t leave adequate space for social distancing when staff walked to and from their workstations.
Rock, however, told PA Post that he could probably install 25 sewing machines on the production floor, with 12 feet separating each machine. He said he planned for 14 people because that’s how many machines he had.
The two men also disagreed about whether masks were a short-term or long-term solution for the company’s challenges.
Rock not only saw the production switch as a way to keep the business out of bankruptcy in the short-term, but he also saw masks as a long-term opportunity. People in the United States wouldn’t want to keep wearing plain white or surgical green masks, he figured. They would want them to be fashionable, so he wanted his business to meet that demand.
But Hoffman thought the switch to masks should be temporary. He said producing them would keep his workers busy while also providing needed supplies.
Hoffman walked off the job on April 16, two weeks after the company received special permission from the state to reopen. If he stayed, he said, he would be forced to implement a plan he thought was unsafe.
The next day, three out of five workers scheduled to sew masks under Hoffman’s six-person plan also left.
Virginia Richmond was one of the workers who left.
She said she was comfortable with five or six people sewing at one time in the room, but not with Rock’s plan to more than double that number with new hires.
“The idea of being around people that I don’t know — I have no idea what their life is like,” Richmond said. “I’m 65. You know, I can’t afford to just throw my life away for a few bucks.”
This is the story of how workers and owners at one small company tried to adjust to the coronavirus upending their business model, navigate the state’s secretive process for deciding which business could stay open, and put in place a safety plan embraced by workers and management alike.
‘I wanted to stick it out’
Hoffman described what happened at All Sports America over the course of several interviews with PA Post, including two video interviews over Zoom and one conducted in-person. Speaking on his porch in the small city of Sunbury, he wore an All Sports America hat and one of the white masks that caused so much conflict at his former workplace.
“I will always root for All Sports,” he said. “I’ve always been a company man.”
Hoffman moved from Pittsburgh to north-central Pennsylvania back in the 1990s because that’s where his brother lived. He started working at All Sports America in the summer of 1998, cleaning jerseys and equipment.
He needed money, and the company was so busy he could pick up as many extra hours as he wanted.
“Youth football was just huge,” he said, referring to the source of so much of All Sports’s business.
By the following January, Hoffman was working full time for the company. He worked his way up to production manager.
In recent years, Hoffman started experiencing more and more problems as a result of a non-combat leg injury he suffered while serving in the U.S. Marine Corps in 1985.
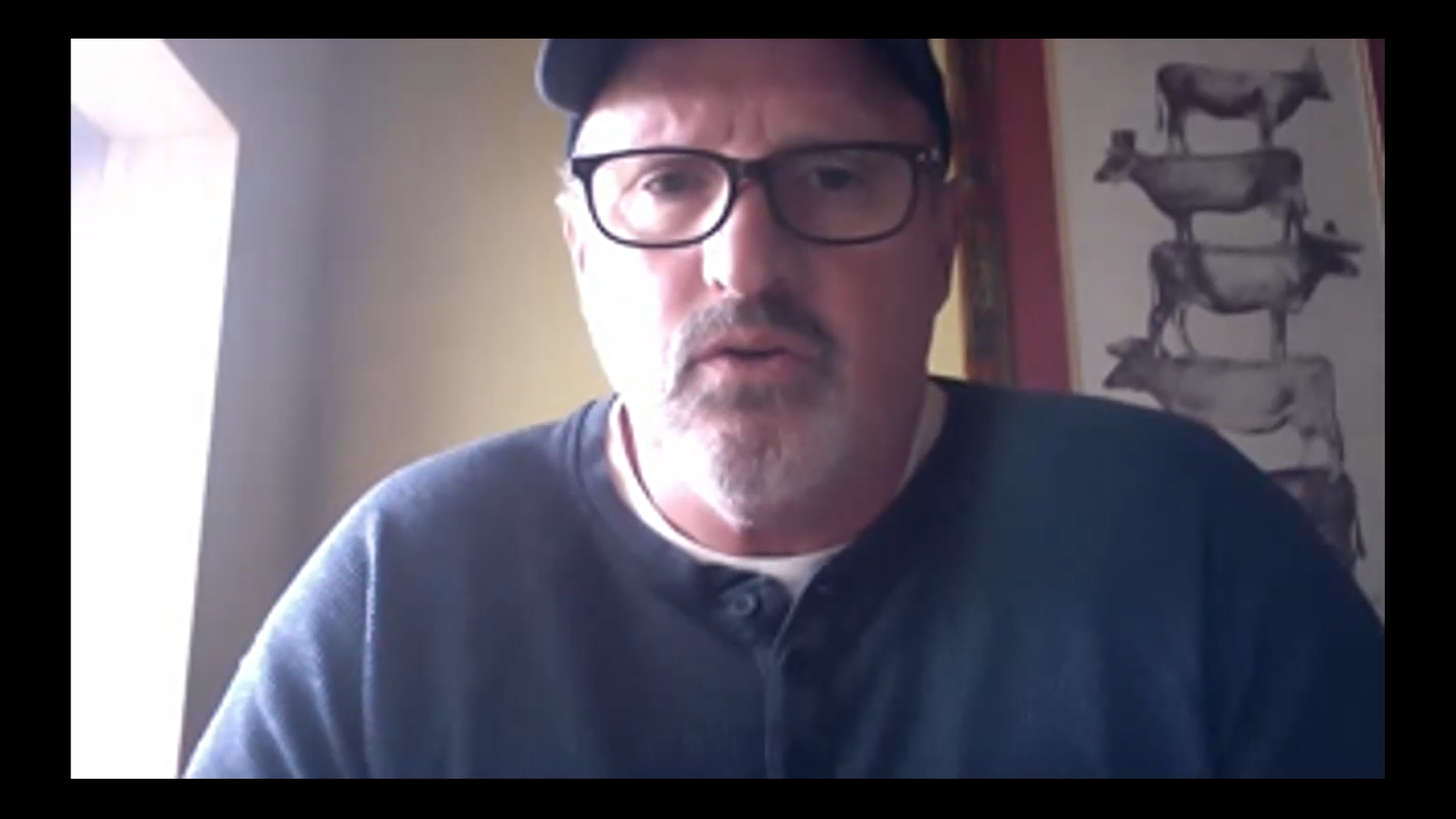
But he said he had a good situation at All Sports America. He’d been there a long time and people knew he would get his work done no matter what, so company officials were willing to make accommodations for his disability — whether that meant he needed to sit at times or even go home to rest. The pay was good: $1,200 a week, he said.
“I knew that I didn’t have many more good years in me,” Hoffman said. “But I wanted to stick it out because I knew the chances of me going to another employer, with my restrictions, was going to be pretty difficult.”
Most of the workers he hired to sew were women in their 60s or 70s, often working seasonally when demand was highest. Pay varied based on their skill level and output — about $12 an hour to $22 an hour.
Hoffman knew the sewing work was tedious, so his approach was hands-off as long as his team got the job done. He and the other workers didn’t hang out after work, but it was a small group, and Hoffman said they felt “pretty close-knit.”
The coronavirus tested those relationships.
‘I’d be bankrupt’
Rock wore a prototype of one of his company’s masks during a recent interview at the company’s plant. The sales section was empty. In the sewing room, football jerseys hung on the walls, and masks — including ones decorated with basketballs, footballs and cats — laid on tables.
Noting the mask, he said he still needed a mechanic to fix a zig-zag machine, so that a mask could be sewn in a way that would prevent it from fogging up glasses.
“It’s really close,” he said. “It’s really close.”
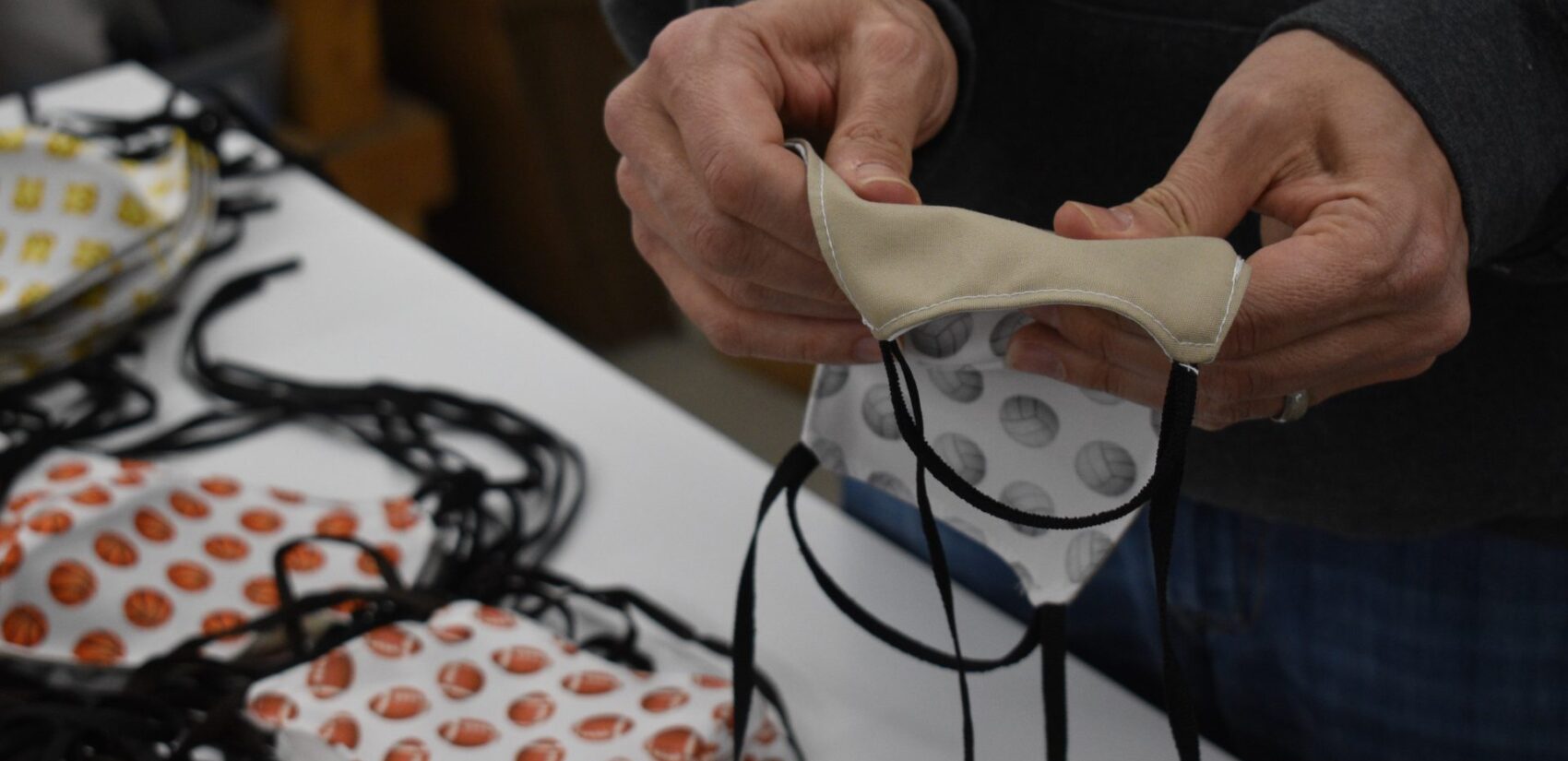
Rock, who started working for All Sports America in 1999 as a credit manager and later became an owner, said he takes the coronavirus threat seriously. He said his wife has a compromised immune system, and that they bought $900 worth of groceries — three carts full — in February to make sure they could practice as much social distancing as possible.
“If I get it, she’s gonna get it, and … she has so many health issues that it would be crazy,” Rock said.
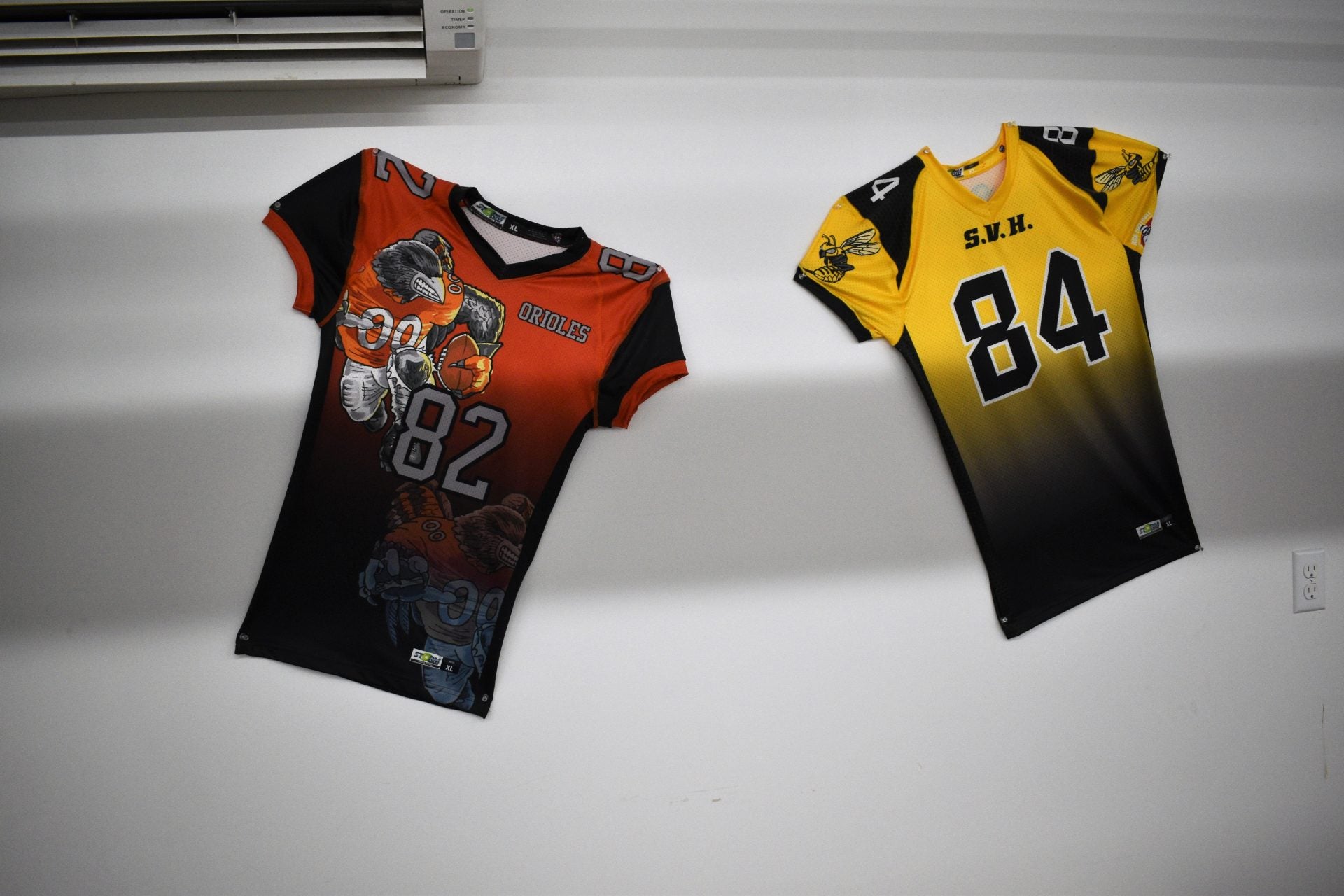
The coronavirus created problems for the company even before the governor’s shutdown order. Its business model relies on selling jerseys and other youth equipment to nonprofit youth organizations run by unpaid parent volunteers.
He doesn’t know when governments will lift restrictions on youth sports, or when parents will feel comfortable allowing kids to participate. “That’s the huge uncertainty,” he said, and why he was quick to embrace the mask idea.
Rock acknowledged that he and some other All Sports America employees worked at the plant between Wolf’s March 19 shutdown order and when the company received its waiver on April 2. He said if they didn’t spend that time working on patterns and prototypes, they wouldn’t have been able to produce masks — which is the reason he wanted the waiver.
“That’s one of those catch-22s,” he said. “I don’t know what people think that, you know, the stuff just magically happens or appears. People have to do something to make it happen. If I didn’t do that, I’d be bankrupt.”
On April 2, before Hoffman knew about the approved waiver, the two men got into an argument at that plant.
At one point during the conversation, Hoffman says Rock told him, “If they get sick, they get sick.” When Hoffman heard that, he saw it as a sign that Rock only cared about making a profit, not about the safety of his employees.
Rock told PA Post that’s not the message he intended to send. He said a lot of frustration led up to that comment, which he said he made after being repeatedly dissatisfied with things he asked for not getting done.
“And so I’m getting tired of the excuses, and my fuse is short,” Rock said.
That argument happened on a Thursday, Hoffman said, and he learned about the waiver approval from the state the following weekend.
Hoffman reached out to four workers that Sunday to describe his safety plan:
- The room would have six stations — anywhere from 12 to 16 feet apart.
- Each sewing station would be cleaned and disinfected.
- Workers would each have their own thread, tools and material to make a mask on their own.
- And there would be no assembly line production to avoid contact with each other’s mask materials.
On Monday, Hoffman and his wife, who occasionally works for All Sports America, cleaned, sanitized and prepped the stations. On Tuesday, workers returned to the building and started sewing masks.
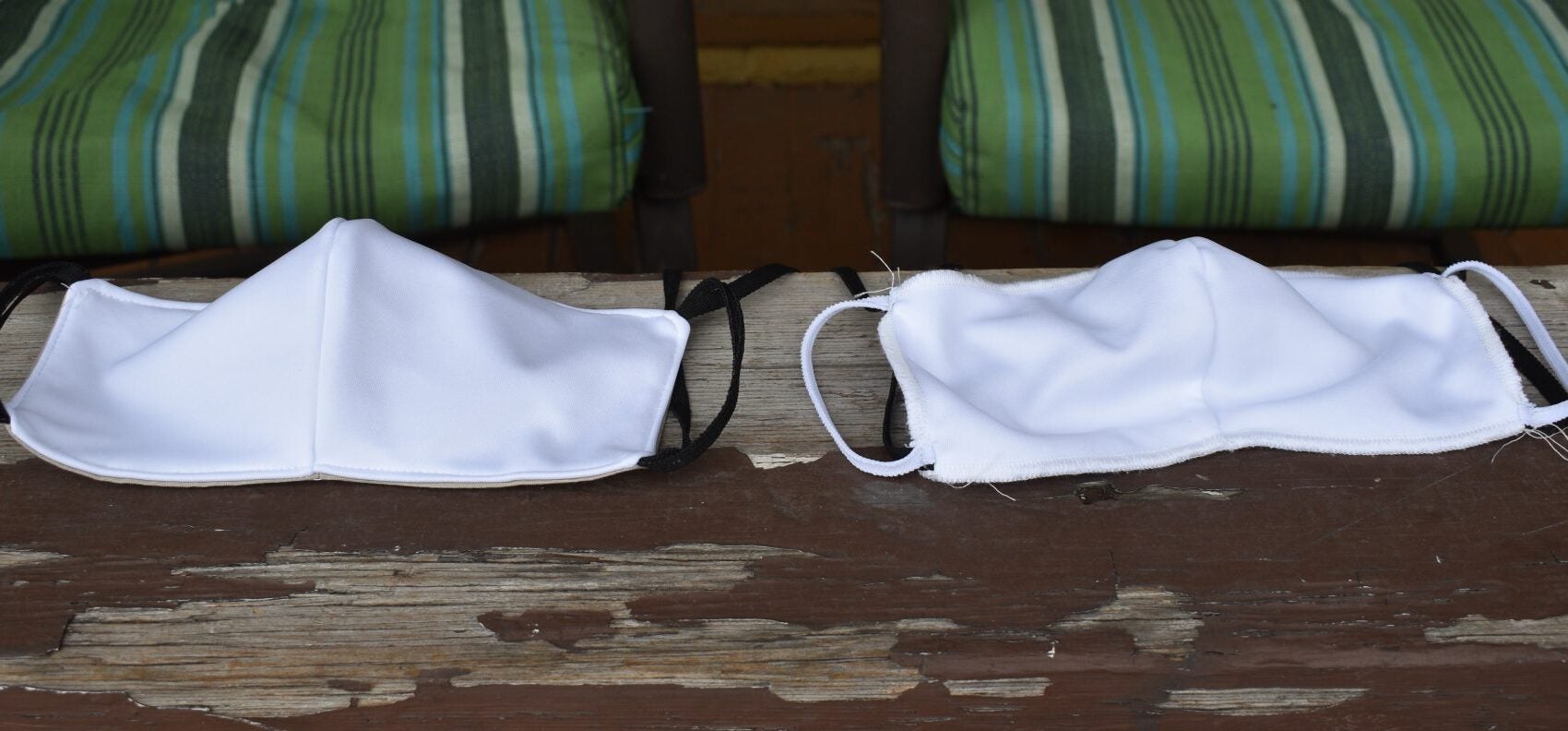
The design of the mask also led to conflict. Hoffman wanted a simpler version that he said one person could sew in three minutes. Rock wanted a more complicated design.
Hoffman said Rock’s version would take two to three times as long for one worker to create and the results would be inconsistent. Rock thought a high-quality product was the only sustainable option.
“And it’s my company,” he said. “So that’s what I’m making and that’s what I want to produce. I don’t want to put out there something that’s fast and easy and simple, and is only going to get me sales today.”
‘I am not quitting’
They never reached an agreement.
On Friday, April 10, the workers attempted to sew the more complicated mask, Hoffman said. By the end of the day, each of them had completed fewer than 10 masks he considered fit for sale.
On Monday, April 13, Hoffman said Rock told him he could safely put 14 people sewing in the room at once, and possibly add another shift — which would mean even more people touching the same equipment.
On Tuesday, April 14, Hoffman said he told Rock that he didn’t think it would be possible to make Rock’s goal of 2,000 masks a day — especially since it had become harder to recruit workers due to fear of the coronavirus and an increase in unemployment benefits.
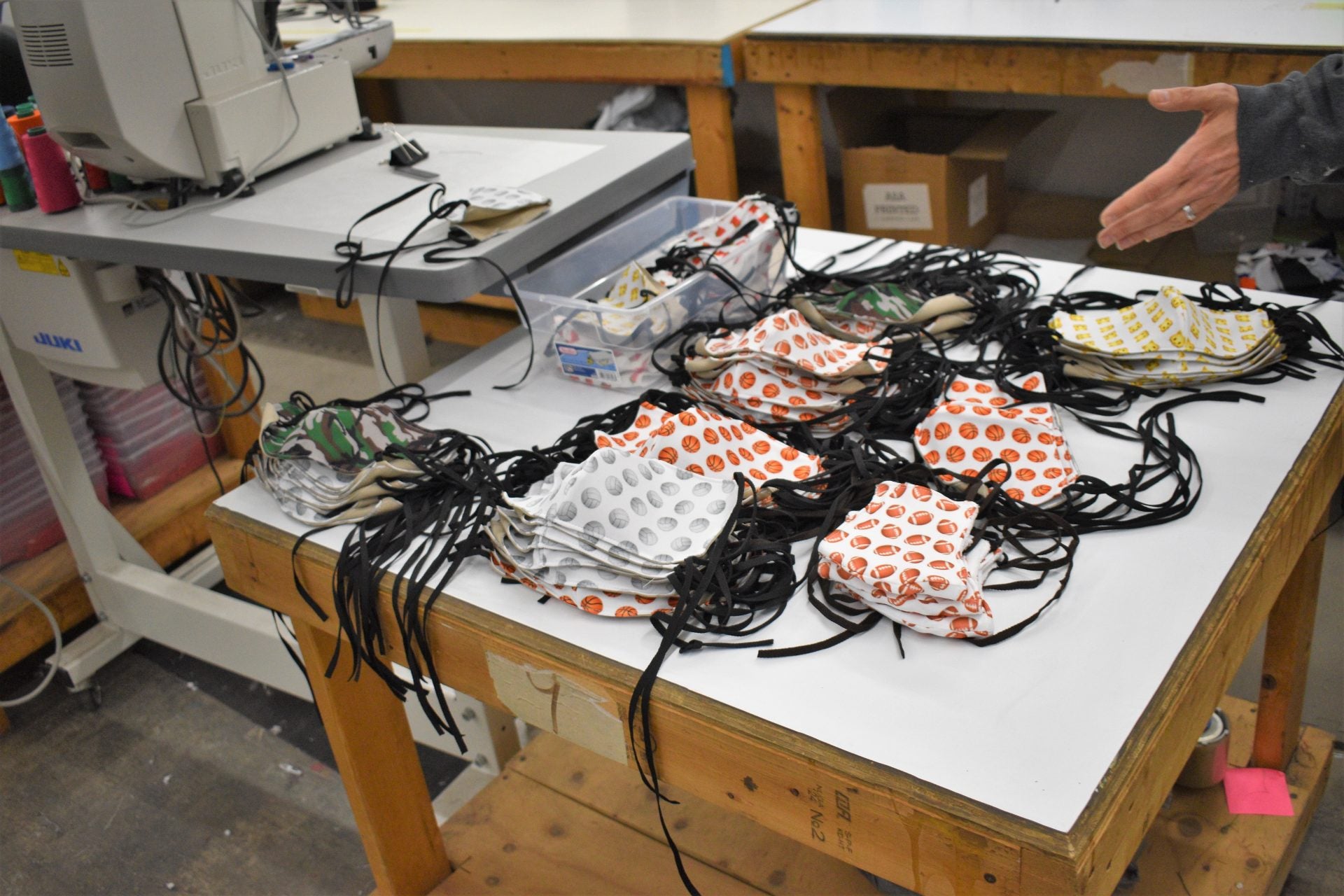
Hoffman thought a 1,000 masks a day could be doable, by possibly adjusting the room to safely add a seventh station and using the simpler version. But Rock wanted to continue with his assembly line plan.
On Thursday, April 16, Hoffman left.
“I am not quitting,” Hoffman recalled saying that day. “But I’m going to leave the building if you proceed with this, because I will not be a part of putting everyone’s life in jeopardy.”
Given the age of most of the workers, Hoffman said they’d be at greater risk of developing severe disease or complications if they became sick with COVID-19. He also has kidney disease and worried about his own health.
By that point, the company had hired a fifth person to fill out the six-person crew Hoffman had originally planned. Rock met with those workers the next day, Friday, April 17.
Virginia Richmond said she was upset that Scott was gone. She didn’t expect him to leave, especially given his leg injury. His absence sent a message.
“It was Scott’s only way of communicating to us that the situation was probably dangerous,” she said. “I know Scott well enough to know that, you know, he is not a foolish person.”
She left. So did two others from the sewing room.
Rock attributed the departures to a lot of fear and uncertainty going around everywhere.
“It’s a scary place right now — a lot of stress all around,” Rock said.
Since then, Rock said he has struggled to hire new workers to fill the sewing room. The company is advertising for sewer/seamstress positions paying $12 to $15 an hour with working conditions that double the recommended social distancing guidelines. But he said that unemployment compensation — including an extra $600 a week from the federal government — makes hiring more difficult.
“I’ve had about 15 people not show up for interviews,” Rock said on April 29. “It’s extremely frustrating, but it’s part of being a small business owner.”
At the time, he was spending about four or five hours a day sewing masks himself, and the crew was able to produce about 1,500 to 2,00 masks a week. They were working on an order of just under 1,500 masks for a construction company in Illinois. A salesman had recently talked to a restaurant chain that wanted to buy 15,000 to 20,000 masks. Meanwhile, a federal Paycheck Protection Program loan was keeping the company afloat.
“I have six-and-half weeks left to try and get production levels up so that we can make enough masks to sustain it,” he said.
A few days later, he was up to three full-time workers and one-part time worker sewing masks, he said in an email. He said he was only planning one shift at the moment.
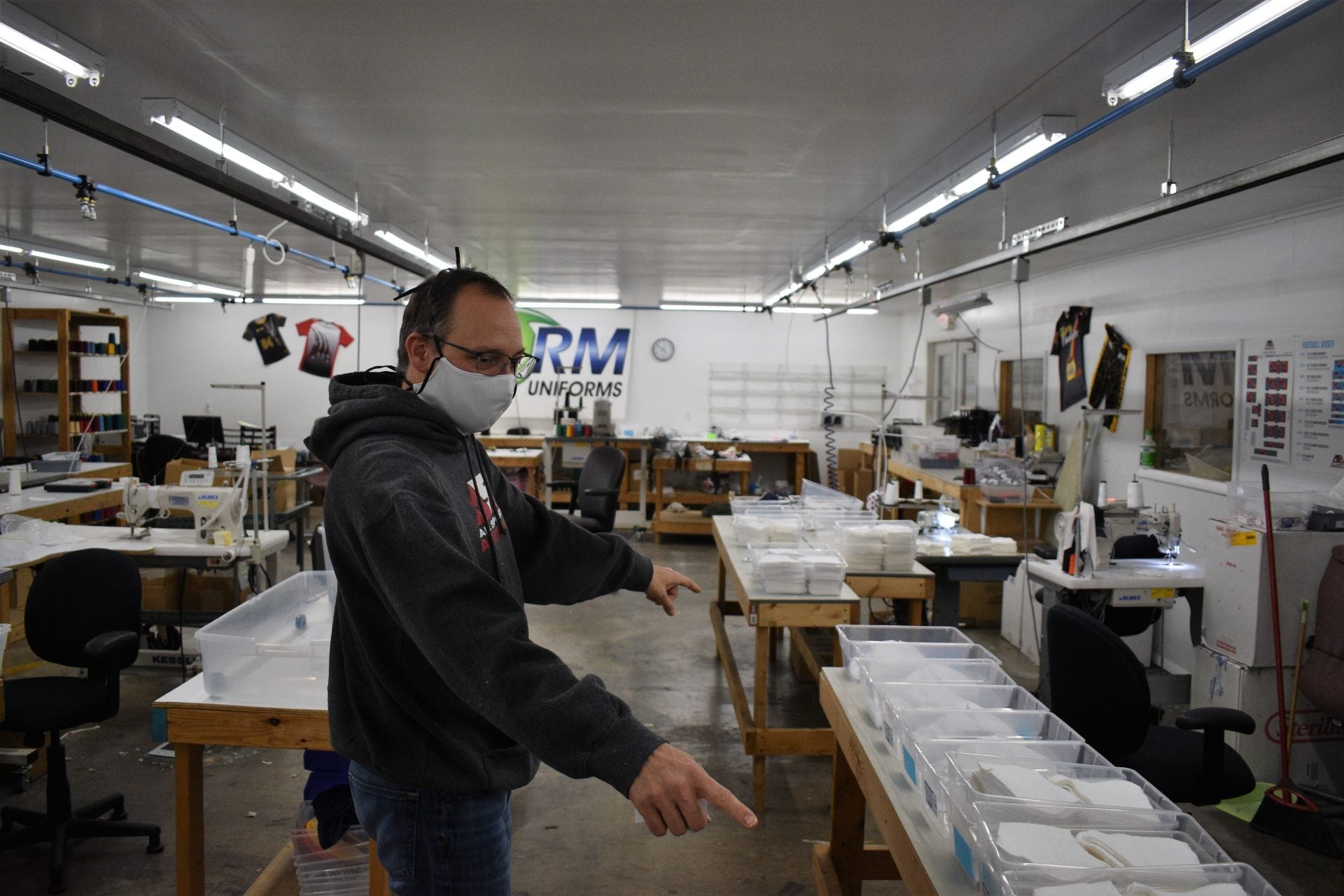
How many employees were allowed?
Even though the company’s first waiver application said it would have less than 10 workers in the building, Rock said he believed he could have more than that. He said he didn’t think there was a limit “as long as I’m not asking them to work on top of each other and to break those types of social distancing rules.”
Smith with the Department of Community and Economic Development gave a similar response.
The state’s April 2 waiver approval said the company was required to comply with “social distancing and other mitigation measures to protect employees and the public … which were submitted with your request and which have been established by the Department of Health and the Centers for Disease Control and Prevention to date and going forward.”
But Smith said that even though the department asks companies to describe the number of employees who would work there if granted a waiver, businesses can have more as long as they follow other social distancing requirements from the Wolf administration for life-sustaining business.
“Our decisions were made based on whether or not the operations would be life-sustaining,” Smith told PA Post.
Hoffman said it “doesn’t make sense” why the company wouldn’t be bound by what it said in its waiver application, and he was disappointed with the department’s response.
“That’s absurd,” Hoffman said.
(The company submitted multiple waiver applications. Another waiver application, which the state approved on April 16, indicated that the company would have 10 workers total in the building, with three people sewing spread out over 2,100-square-feet, according to Smith. Hoffman said he never saw that waiver application.)

‘The most powerful thing’
All Sports America no longer needs a waiver to stay open.
Northumberland County, where it’s based, was one of 24 in Pennsylvania that had some restrictions lifted at 12:01 a.m. Friday. The county has 125 total reported coronavirus cases and no deaths, as of Monday.
But concerns about employee safety will continue. The Department of Health launched a tip line for people to make complaints about business on April 21, five days after Hoffman walked off the job. Department of Health spokesperson Nate Wardle said more than 7,000 complaints have been filed. He said many of the complaints are inappropriate or “prank complaints,” but he offered no specific numbers. He said some letters have been sent to businesses in response to complaints but declined to say how many.
Last Tuesday, the governor said the state doesn’t have the resources to actively check that every business is complying with worker safety requirements.
Wolf said employees who don’t feel safe should tell their employers, and they can also turn to local, state and federal agencies.
“And in the end, they have the ultimate sanction, which is just to say, well, then I’m not coming to work,” Wolf said. “And as a former employer, I know that would be the most powerful thing that any worker can do.”
That’s the path Hoffman chose.

After Hoffman left, he said he spent about an hour-and-half calling the state’s unemployment hotline over and over again. He did manage to reach someone. He said he explained why he left All Sports America, and he’s waiting to receive benefits.
Sitting on his Sunbury porch recently, he said he planned to look for a new job. If he can’t find one, he’ll apply for federal Social Security disability benefits.
He said he wishes he was still working at All Sports America, but he doesn’t doesn’t regret leaving for the reasons he did.
“Normally, if they gave me something hard to do, I would just say, all right, I’ll give it my best and try,” Hoffman said, “but this time, I said, no, no.”
WHYY is your source for fact-based, in-depth journalism and information. As a nonprofit organization, we rely on financial support from readers like you. Please give today.